Universal Robots just released the UR20, the newest member of the UR cobot family. When designing the UR20, they undoubtedly considered palletizing.
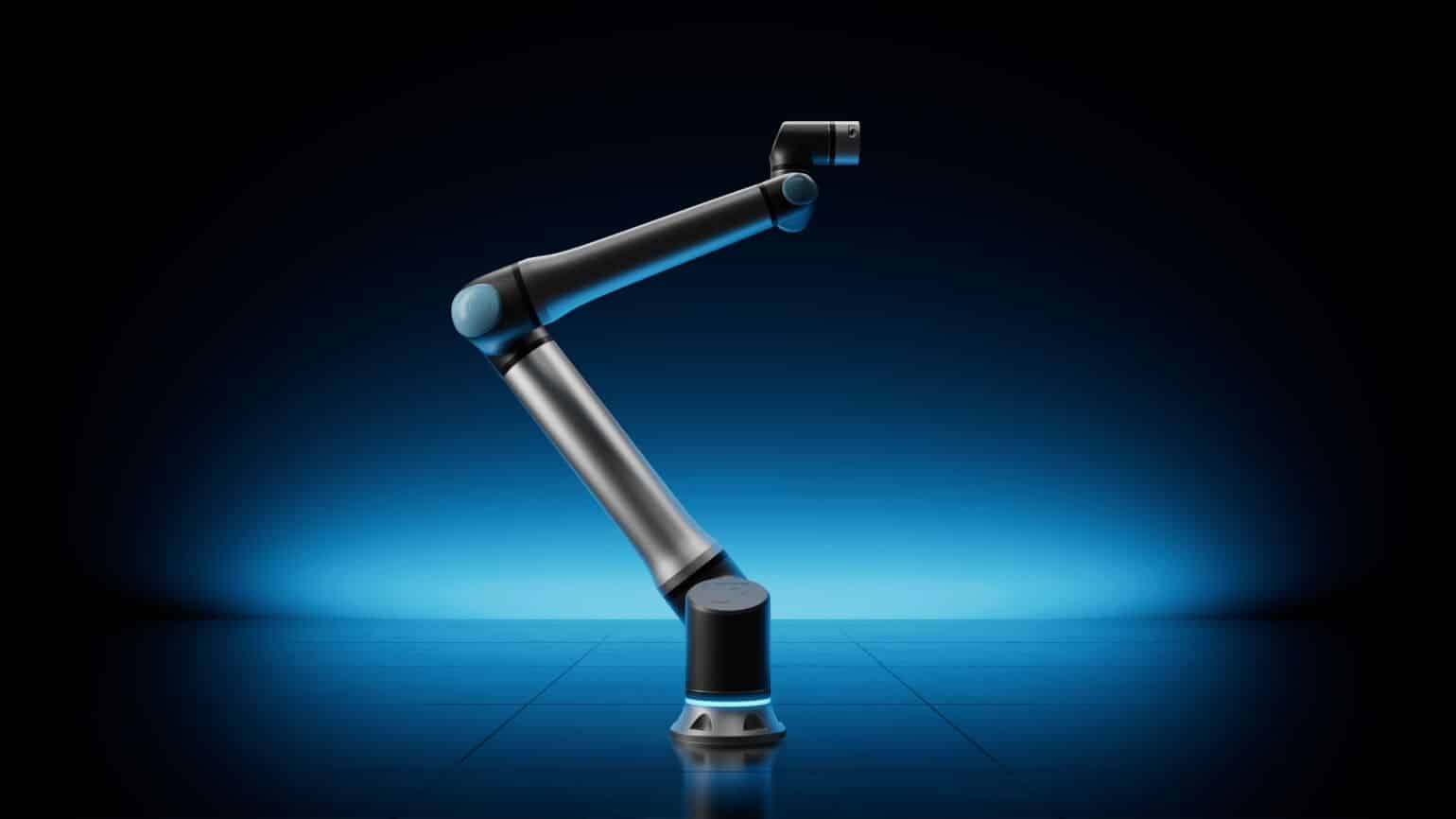
Having worked with UR for palletizing applications for seven years, we have examined the details of what we know and what we don’t know. We assume the UR20 will contribute to the palletizing space.
Safety is a key factor in palletizing, and in many cases, a larger robot enhances operational safety. We’ll explore why size matters and how it improves efficiency. Additionally, automation offers huge benefits, making palletizing more accessible for SMEs through collaborative robot solutions.
In this analysis, you’ll learn why Rocketfarm believes the UR20 is a strong choice for palletizing automation, its potential contributions to the market, and its limitations.
Do you want to learn more about the UR30 as well? Then check out this article.
The UR20 Cobot Explained
The UR20 is the newest addition to the robot quiver from Danish Universal Robots (based in the robotic hub of Odense). It’s a larger collaborative robot with a payload of 20kg (in the full range of motion) and a reach of 1750 mm. Learn everything you need to know about UR20 and its specifications here.
In this article, we will focus on the possibilities for UR20 in palletizing, as this is our expertise. We have worked with Cobot Palletizing and Universal Robots since 2015, and our Pally software is the market leader in this sector.
In many palletizing situations bigger is safer, and the new possibilities with UR20 are a welcome addition to the market of collaborative palletizers.
Halvor Gregusson
Technology and Innovation Strategist at Rocketfarm
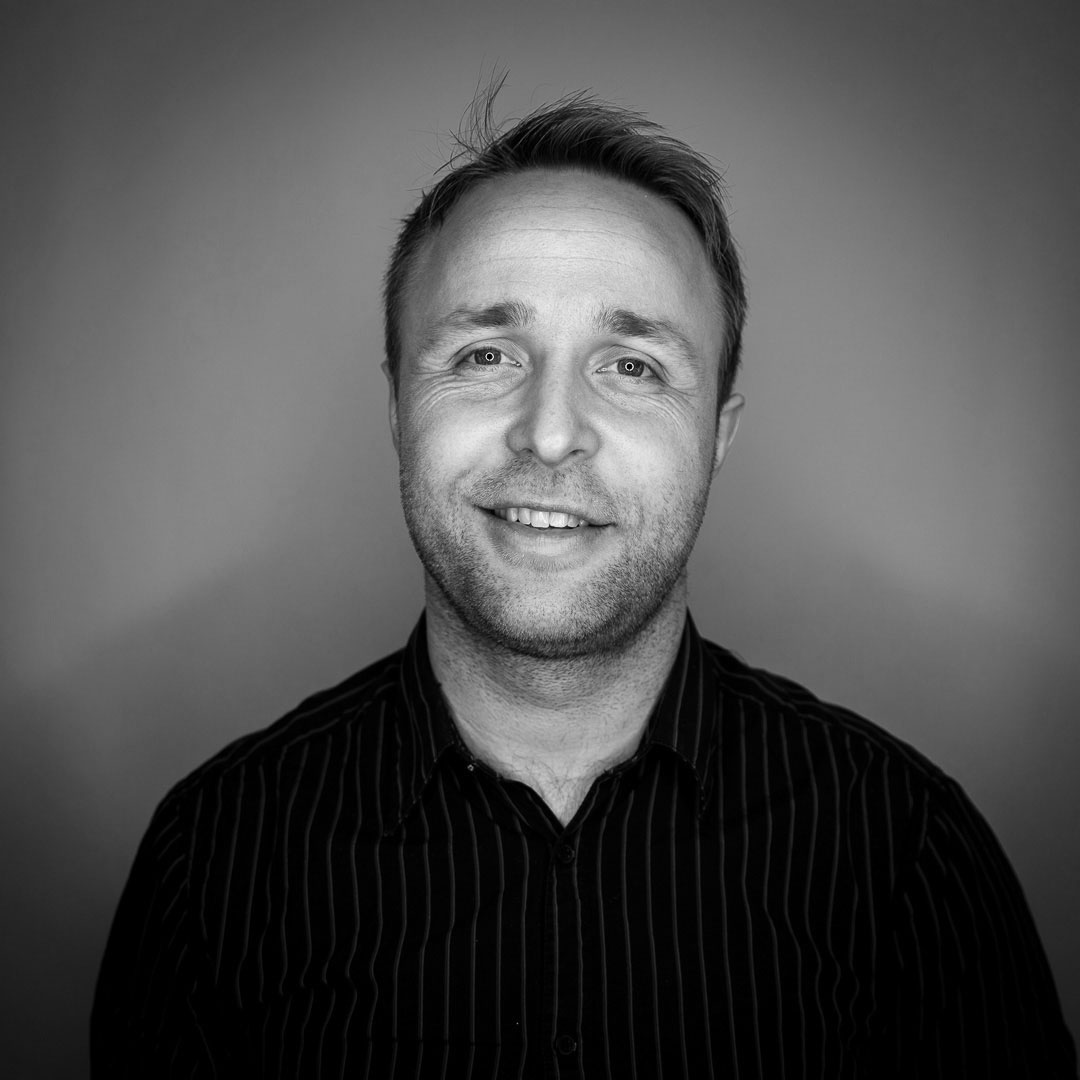
Cobot Palletizing 101: A Quick Introduction
So, in short, palletizing is the process of stacking products from a conveyor belt to a pallet. Depending on product specifications and production speed, this task is performed manually with palletizing machines or palletizing robots. Additional specifications like height, width, and stacking pattern of a complete pallet are also essential to analyze before choosing the right palletizing solution for a production line.
Collaborative robots, or cobots, are usually used when the production speed is below 30 products/min, and the product weight is within the cobot’s payload capacity (with UR20, anything below 20 kg).
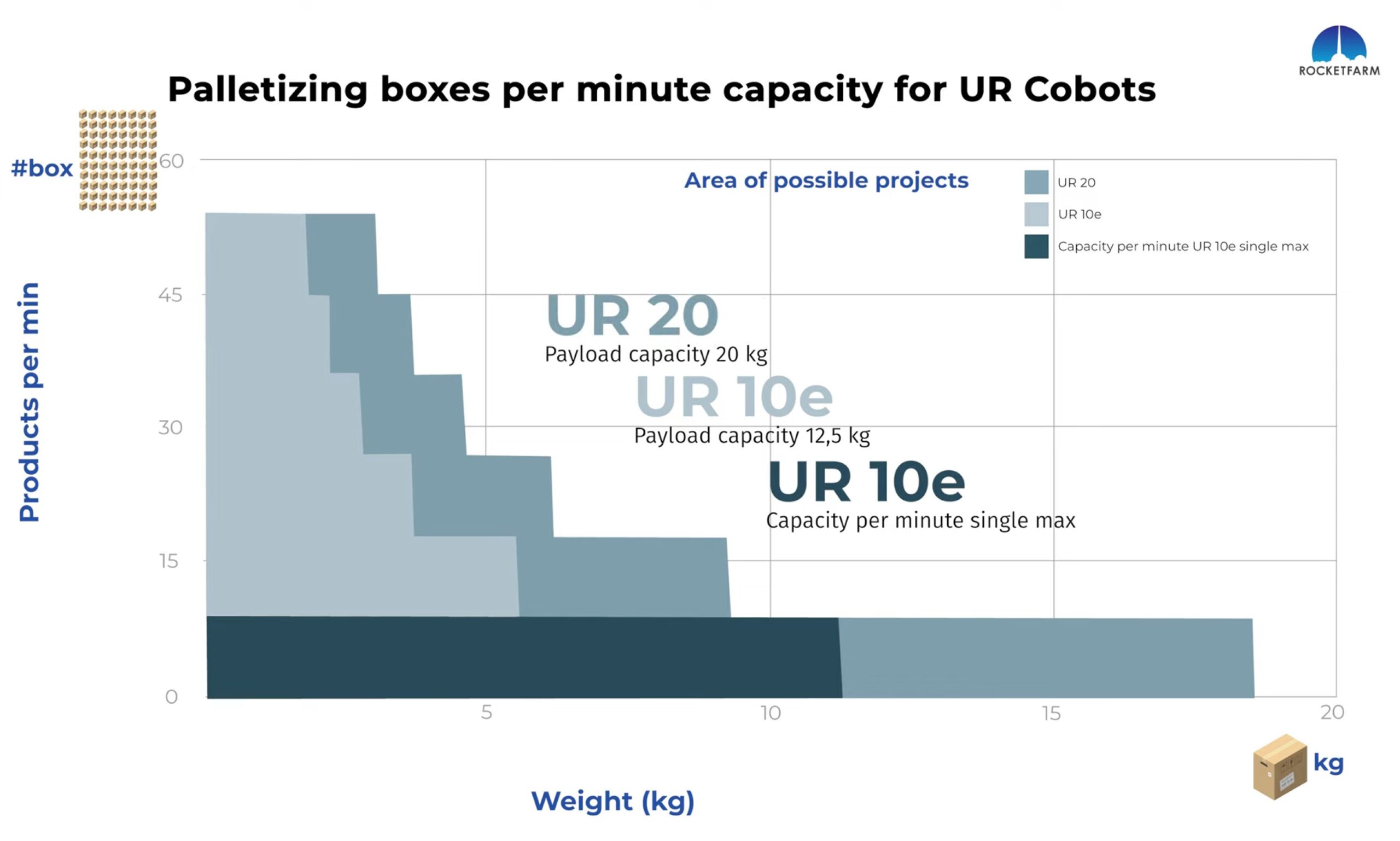
UR20 for palletizing
As mentioned at the beginning of this article, we believe that the UR20 is a very suited robot for palletizing. And it’s not just us. Universal Robots has also highlighted the possibilities of palletizing with UR20.
There are several reasons why UR20 seems to be designed for palletizing. Below, we will explore the details of the cobot to analyze everything we know about the UR20, particularly in relation to palletizing, which is an area in which we have extensive knowledge.
If you’re eager to know more about the difference between a cobot and a robot palletizer, you should read this article: Cobot vs robot palletizer – what to choose? | Rocketfarm
For anyone familiar with Universal Robots’ naming convention, UR20 stands for 20kg payload. With a payload capacity of up to 20kg, it “only” exceeds the UR16e with 4kg extra payload capacity, but for cobot palletizing applications, another feature that makes it far superior to its predecessor is that it is bigger! A lot bigger!
With a reach of 1750mm, it outperforms both the UR16e and the UR10e by a landslide. It is the combination of payload and reach that turns the UR20 into a palletizing cobot by design.
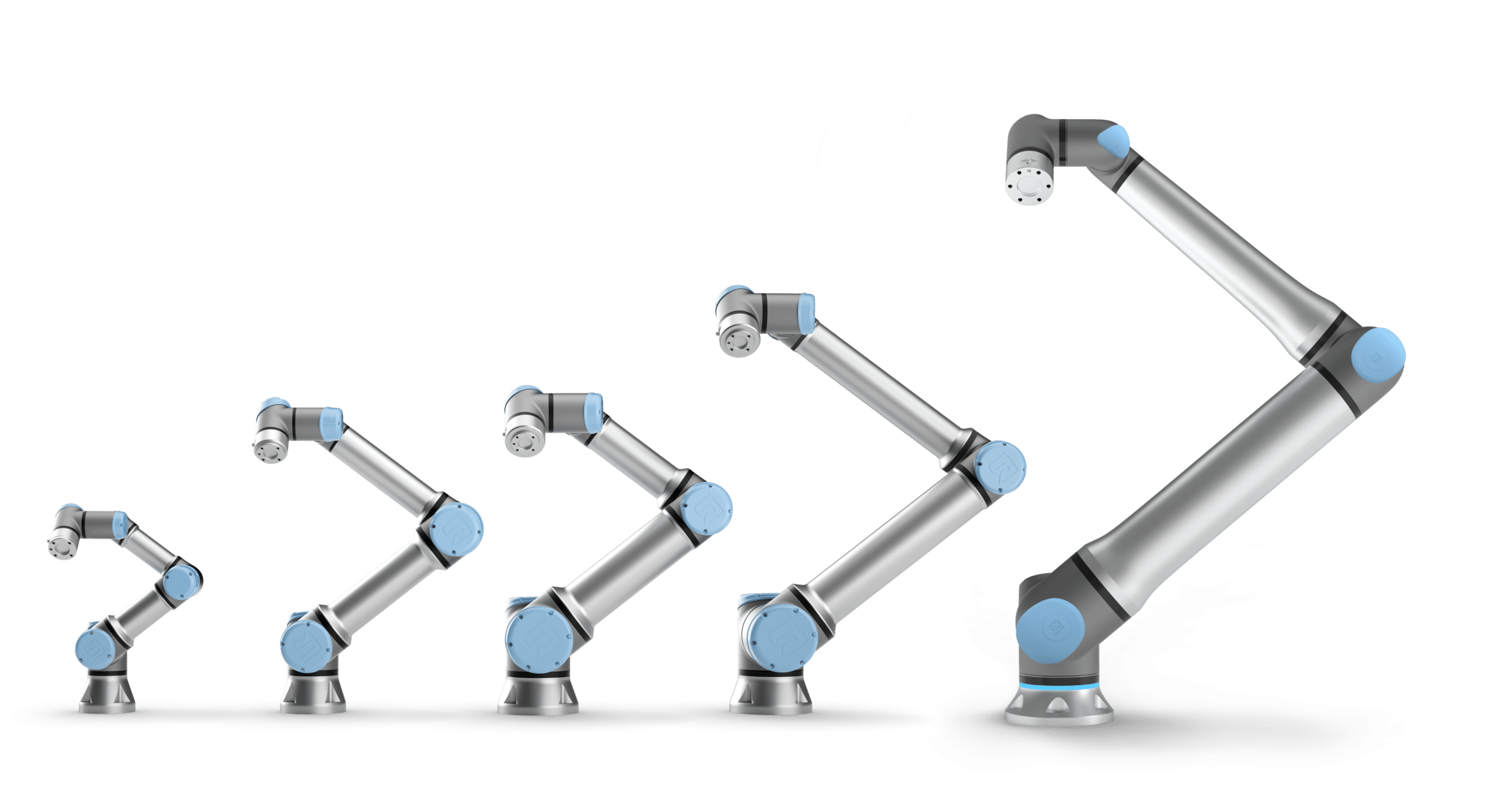
UR20 vs. UR16e
Let’s compare the UR20 to the UR16e as an example. Although the Universal Robots community heavily underestimates the UR as simply “too short” to reach the far corners of a pallet, it does have its natural limitations when stacking taller and wider pallets, which is particularly true for the US compared to the EU standards.
Even with extensive use of a separate 7th axis (lift), our assumption is that the UR16e is simply perceived as “too short” by the community. As a result, the UR16e has never really been considered for palletizing.
UR20 vs. UR10e
The UR10e, on the other hand, is, in many scenarios, a great palletizing cobot.
For a number of scenarios, especially when working on EU1 pallets, the reach is long enough to manage without a 7th axis (something that can easily be verified through Digital Twin Simulations).
Using a 7th axis will provide the necessary reach for practically all palletizing scenarios, given that you use palletizing software capable of optimizing reach due to gripper orientation at grab and release.
However, contrary to its name, its payload capacity is “only” 12.5kg. There is a considerable gap between 12.5 kg and 20kg in palletizing.
Despite what you may think, there are several reasons why this payload gap from existing UR cobots to UR20 represents so much more than the few kg difference.
Bigger is Safer
First, let’s point out a key selling for any robots.
There are several tasks that humans simply shouldn’t do. Picking and placing boxes of 10kg from a conveyor belt to a pallet is already in the pain point area of what will wear a worker out. Moving into the 10kg to 20kg area of payloads, we are in the zone of heavy human labor. Being a palletizing cobot for this interval, the UR20 is solving more than swapping people with cobots. It will perform in a time frame that is considered much more painful to humans.
From an “industrial robot” point of view, more payload and reach is usually linked to “more power” or “stronger”, with a natural line of thought that it also becomes more dangerous if it hits a person or you get trapped by it.
However, UR20 is still a cobot. This does not mean it can’t hurt you if it hits you, but it will stop IF it hits you. So what makes this different from a UR10e, you wonder?
Same Polyscope Version
First, what is not different from a UR10e? Keep in mind we are talking about palletizing applications.
What we do know is that the UR20 will be running on the same Polyscope 5 as the UR10e. This means that the features from UR10 are also available for UR20. With this feature set, you can easily configure safety planes that the robot will, certifiably, not exceed.
An example of what you can do is reduce the operation area to be equal to the UR10e. By using this feature, the extra reach does not represent a bigger area of operation for the cobot.
Collision Energy is Key
Secondly, what is different from a UR10e? Still, keep in mind that we are talking about palletizing.
Due to the fact that the cobot stops if it hits you, the danger of a cobot is much more linked to the collision energy of the system than the force it can push a person towards a barrier.
Hence, the collision energy of an impact is key to determining the hazard level of the application. To simplify the “ISO 15066 Robots and robotic devices — Collaborative robots”, the collision energy of the system follows the equation:
E=1/2mv^2.
It may not be evident at first glance, but what it really tells you is that the speed of the system is, for this scenario, almost everything that counts.
And here’s the catch: Extra payload can be transferred into slower speed, thus far less collision energy.
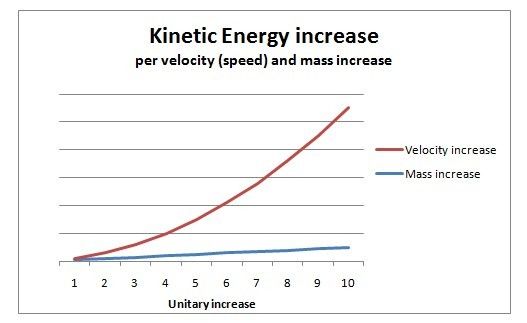
Let’s Do the Math
Let’s investigate it with an example. Let’s say you require a 6kg product to be palletized at a required nine products/minute pace onto a pallet (if you only want the result, not the explanation, simply skip the following two paragraphs):
For this equation, m refers to the complete mass of the system, including the weight of the cobot. (For simplicity, we use the entire weight of the UR10e, 35kg, and the UR20, 65kg.)
To do this with a UR10e, you would need to achieve a maximum speed of the system of at least 1.5m/s. Due to the payload limitations, and given the fact that at least 1kg of the 12,5kg capacity is needed for the gripper, this only leaves 11kg payload capacity, hence with 6 kg, the cobot can only grab 1 product per cycle.
This gives the following equation E=½ (6kg + 1kg + 35kg)*1,5m/s^2 = 47,25J.
Using the exact requirements with a UR20, you can pick three products for each robot cycle, meaning you would only need to move at a maximum speed of 0,5m/s. Let’s say we also need to add 1kg extra to the gripper to multi-pick several products, but we are still within the 20kg limit.
In this scenario, the equation looks like this. E=½ (18kg + 2kg +65kg)*0,5m/s^2 = 10,63J
Comparing the Scenarios
Comparing the two cobots, solving this scenario with the UR10e, we have a potential system energy of 47,25J. To give you an idea, this is equivalent to the energy of a baseball pitch of an “average 12-year-old league pitcher” in the US. Or said differently, if you have a 12-year-old son pitching for the local baseball team in the US, and he pitches averagely fast. If you stood next to him and he accidentally hit you with his average pitch, that represents the same collision energy of the cobot in this scenario.
The same requirements solved with a UR20 only add up to 10,63J. Almost a fifth of the energy!
Safety Depends on the Scenario
Safety depends on the scenario. Most often the right questions is not “how fast can the cobot move“, but “how slow can the cobot move and still make the speed requirements“.
Halvor Gregusson
CIO at Rocketfarm
Compatibility with Other Systems or Components
We do not know if Universal Robots has hidden some new “gems” for us in the UR20, but we do know it will run with the familiar Polyscope 5 interface and that existing URCaps will work on the UR20 as for the UR10e. But no news can also be good news. It means that UR’s comprehensive list of supported components through their UR+ ecosystem will also be available for the UR20.
An important detail, though, is that to be able to deal with heavier payloads, UR has increased the size of the tool flange (connection point for grippers/tools, etc). So, there will be a need for an adapter if you have to work with tools made for any of the older robots (UR3e, UR5e, UR10e, or UR16e).
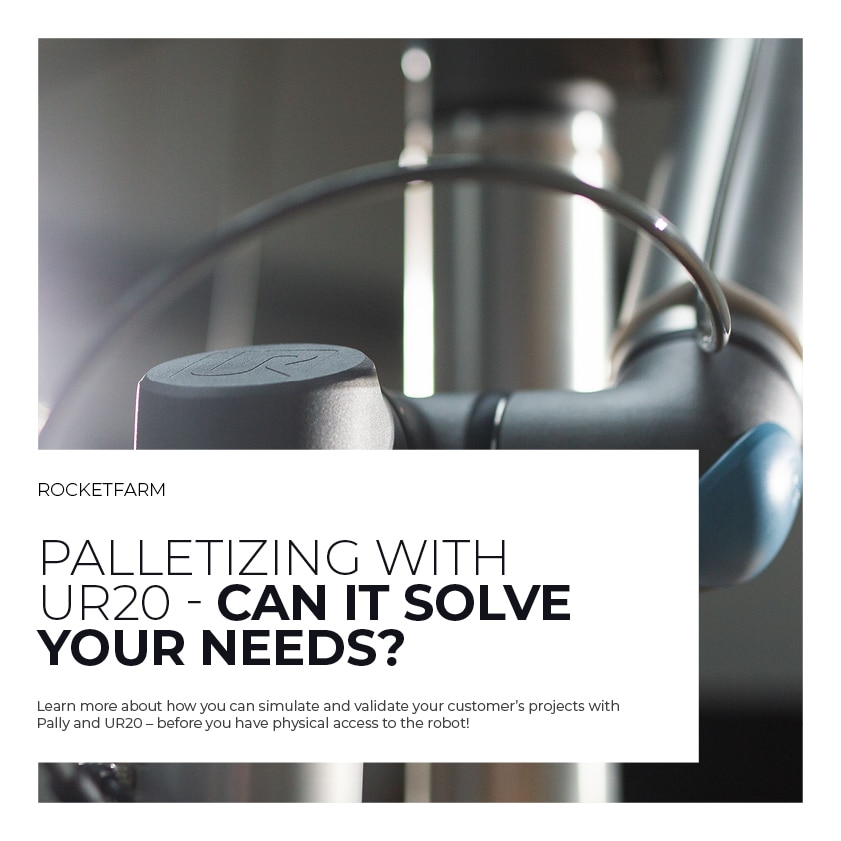
Keep reading or download our free UR20 Ebook to learn more
Wear and Tear
Little is currently known about the hardware components used in the UR20, except Universal Robots has stated they have redesigned this robot from scratch, removing 50% of the parts to ensure robustness.
Assuming, though, that they will still be using the Harmonic Drive gears, these gears have an expected lifespan of 30,000 hours of operation in the previous UR cobots.
That, again, follows from an expected use level of the robot, which can be said to be a “rough” use. Treat the cobot nicely, and it will behave nicely in return. Although having suffered a bit with their CB1 and CB2 series with respect to some quality issues, the UR cobots have been high quality since their CB3 series release.
What to expect from the UR20 is unknown, but we know the laws of physics. Just like low speed reduces energy levels in potential collisions, low acceleration reduces the tear and wear level of “any” mechanical joints with friction, which is precisely how a robot is designed.
Hence, reducing the max robot speed reduces the need for max acceleration, reducing the cobot’s tear and wear. With the higher payload capacity, you can more often pick more products per pick, hence you can reduce overall speed, acceleration and tear of the cobot.
Hence, reducing the maximum speed, reducing the need for maximum acceleration, and reducing the tear and wear of the cobot.
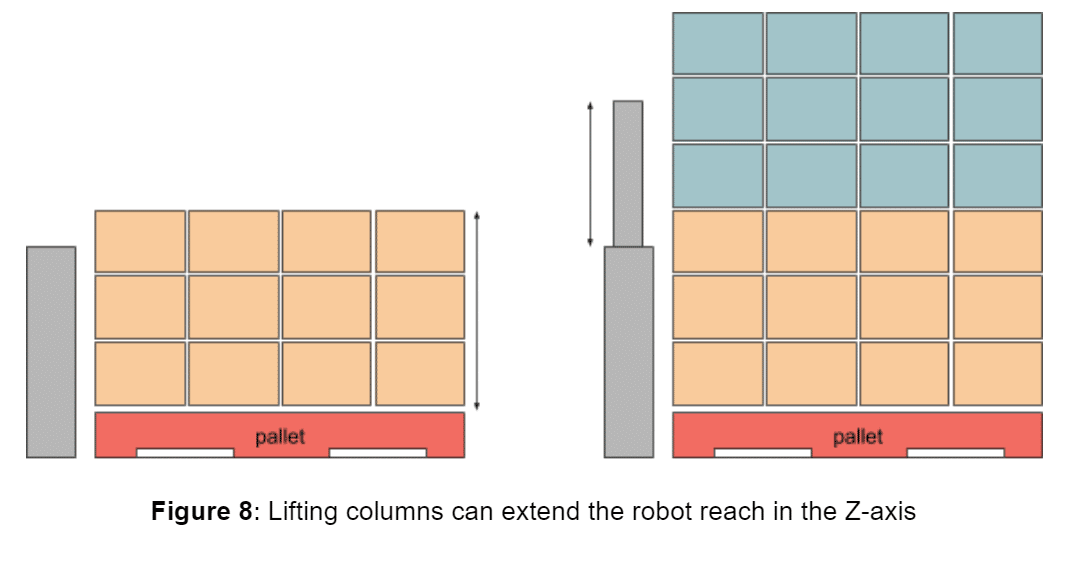
Removal of the 7th Axis (Lift)
The UR20 has an extended reach, which should allow it to palletize without the need for a seventh axis. While fewer moving parts are generally a good thing and can contribute to a lower overall cost of the system, it does not necessarily mean lower complexity in the solution.
On the positive side, eliminating the need for a 7th axis also removes a potential risk of pinch points arising from the movement of the lift rather than the robot. While the cobot has certified mechanisms for stopping when hitting something, this functionality may not be true for all lifts. If you plan on designing a palletizer for yourself, make sure the lift has certified functionality for stopping if the “protective stop” signal in the cobot is triggered.
From an engineering perspective, with a 7th axis, you always have the option of moving the cobot to a more favorable position to grab a product from the conveyor belt or release it on the pallet. With a fixed position, this “luxury” is not present, and the cobot’s path planning needs to take this into account. This adds complexity to the path planning and increases the probability of collisions in the palletizing process.
An example of this for the UR20, compared to the UR10e, is that you will need to take into account the extra length between the shoulder and elbow joint of the cobot. The elbow is more likely to collide with a fully stacked pallet on the left side while palletizing on the right, and vice versa.
Either way, you will need more optimized path planning, or you will need to move the pallets further apart, increasing the overall footprint of the solution and reducing the maximum palletizing height of the system.
Programming
As mentioned, UR20 will be available with Polyscope 5 with support for existing URCaps. Whether you are considering purchasing a cobot palletizer or designing one based on the UR20, there are a few things to be aware of compared to a UR10e.
First things first. For various reasons, think twice, and twice again, before even considering “the old way” yourself – programming line by line, each product placement of the pallet.
Universal Robots has a free template script for palletizing, which is a far better option to experiment with. However, for a number of reasons, we strongly recommend looking into more specialized, “no-code” software for palletizing, like Pally.
Advanced Choices, Simplified
As mentioned above, the right question is not “How fast can the robot palletize?” but “How slow can the cobot move and still meet the requirements?”
Choosing a software enabling the ability to switch between multi picking of boxes and single picking boxes based on pallet layout is not only a potentially faster option, it is also the safer option.
Though this certified safety level step also applies to the UR10e, the UR20’s capability to pick multiple products more often makes it more significant for the UR20.
Setting the certified safety level in the cobot to correspond with the pace at which the palletizing software/program can deal with the production speed is probably the most important, easiest and cheapest safety measure you can do.
Halvor Gregusson
Technology and Innovation Strategist at Rocketfarm
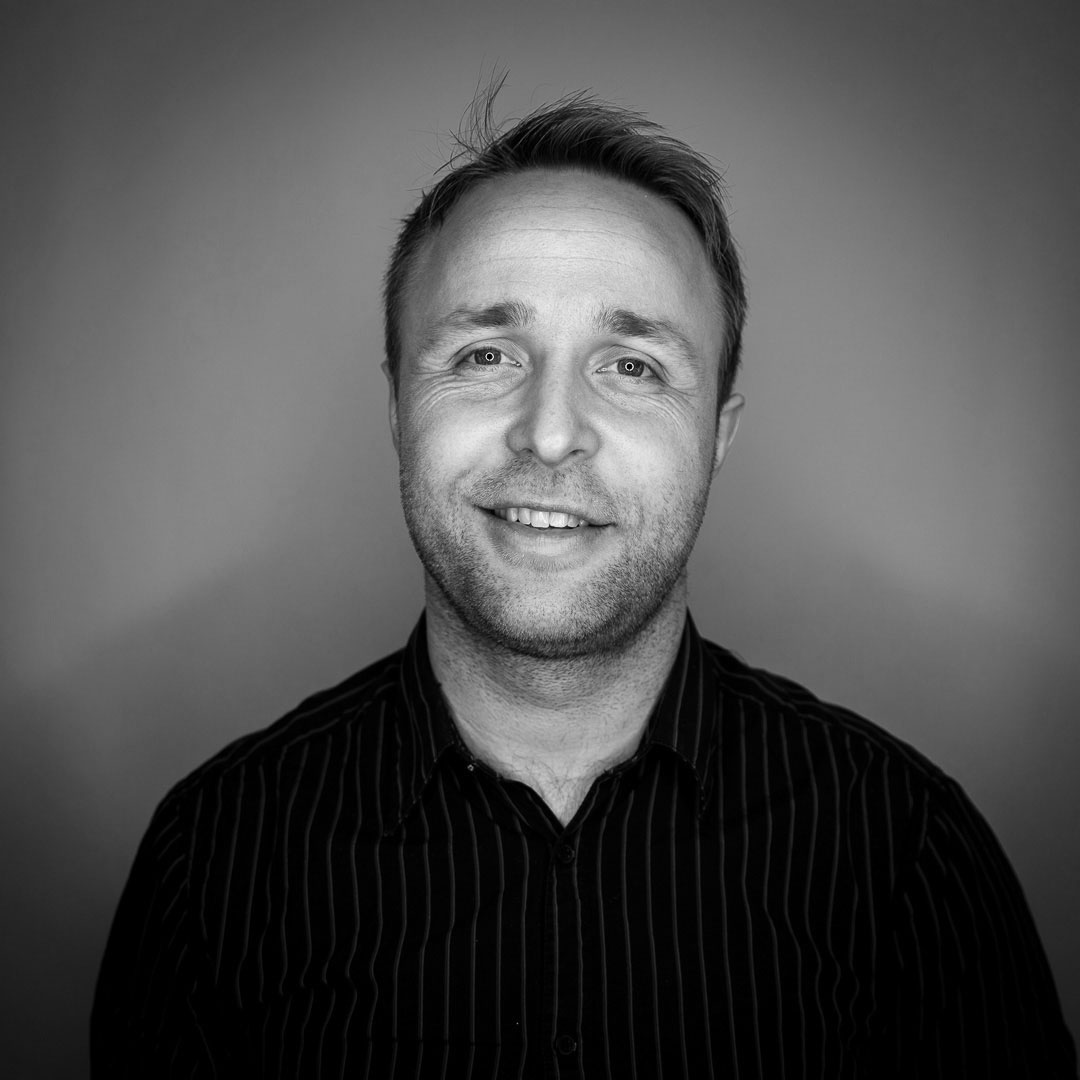
Make Post-Installation Changes with Flexibility and Ease
Secondly, with the UR20, the cobot can palletize a greater variety of products, meaning more frequent product changes and post-installation changes. In our experience, manufacturers will find themselves quite annoyed with solutions that require extensive knowledge of programming skills to add new products or pallet sizes. They often encounter problems as “the one who knows it doesn’t work here anymore.”
Reach Issues Remain Complex
Third, the extra reach of the UR20 is definitely a huge advantage. Still, the added complexity that comes with removing the 7th axis can, for many scenarios, make it more challenging to reach the far corners of a tall pallet and avoid collisions when palletizing close to the cobot.
Bluntly stated – the UR cobots have an easy interface to program simple pick-and-place applications.
Palletizing, on the other hand, is actually a far more complex process. Don’t underestimate this. You will soon find yourself spending far more money than what you saved by choosing DIY, free software, or so-called “turn-key solutions” with a stronger emphasis on hardware choices than software implementation.
Choose a palletizing solution with a designated software. It pays out in the end. Choosing a palletizing solution without software is like purchasing a brand-new laptop and realizing it runs on MS-DOS.
Mobility
If we were to state a weak point for the UR20 compared to the UR10, it would be mobility. While the UR10, with its 35kg, frequently has been added to solutions that are easy to move between production lines, the UR20 is far more “clumsy.” We expect the UR20 to be planned for more fixed installations. We don’t expect to see many UR20s driving around on MIRs or other automated vehicles.
That said, in our experience, while mobility is usually a good selling argument, most end customers who like the cobot would rather start planning a second cobot than move around the one they have.
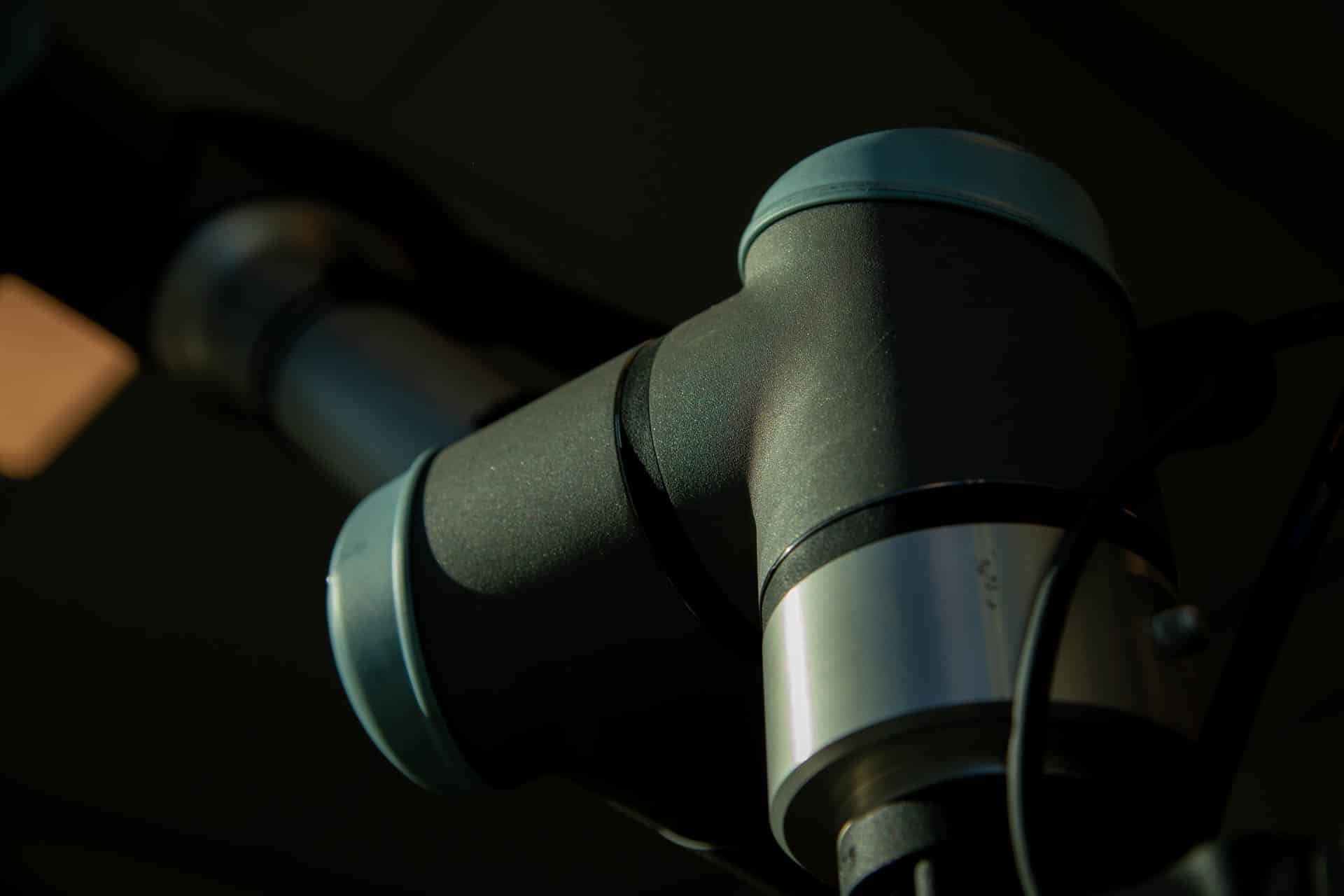
Start Planning? Simulate It First!
The digital files, such as 3D models and control software, will make it possible to plan, program, and test the cobot in the digital world.
Whether you are a manufacturer looking for a cobot palletizer or you are about to design your standardized palletizing solution for the market, we strongly recommend that you look at what options are available to do good simulations of a real-life scenario.
Over the last two years, Rocketfarm has done close to 700 Digital Twin Simulations for feasibility and sales purposes for end customers, distributors, and system integrators of palletizing solutions running on Pally software, which currently powers more than 200 palletizing cobots globally.
If there’s one thing both we and the receiver of these simulations have learned, it is that accurate simulations are by far the most efficient method to reduce upfront risk and achieve internal trust with whoever is supposed to purchase a cobot palletizing solution.
Insights, Challenges, and Key Comparisons
Feel free to reach out if you would like us to analyze your specific project or palletizing needs.
Brigt
Channel Executive at Rocketfarm

Sign up for our newsletter and get a FREE ebook
By signing up for our monthly newsletter, you’ll get case stories, product launches, and tips to automate your production line!
Additionally, you will instantly receive an ebook about implementing palletizing. For more information, please visit our newsletter subscription page.
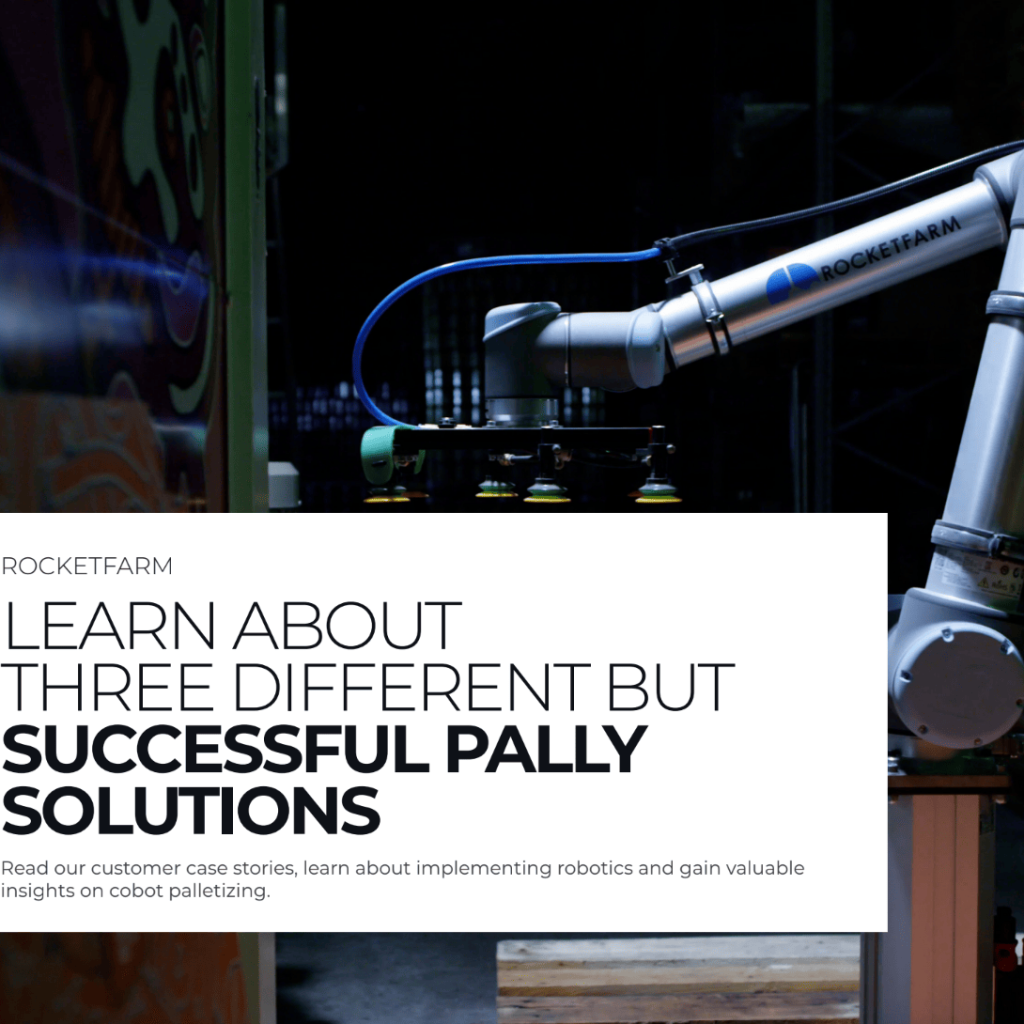