Are you interested in buying a cobot depalletizer? Rocketfarm makes it easy
to get started with dPally.
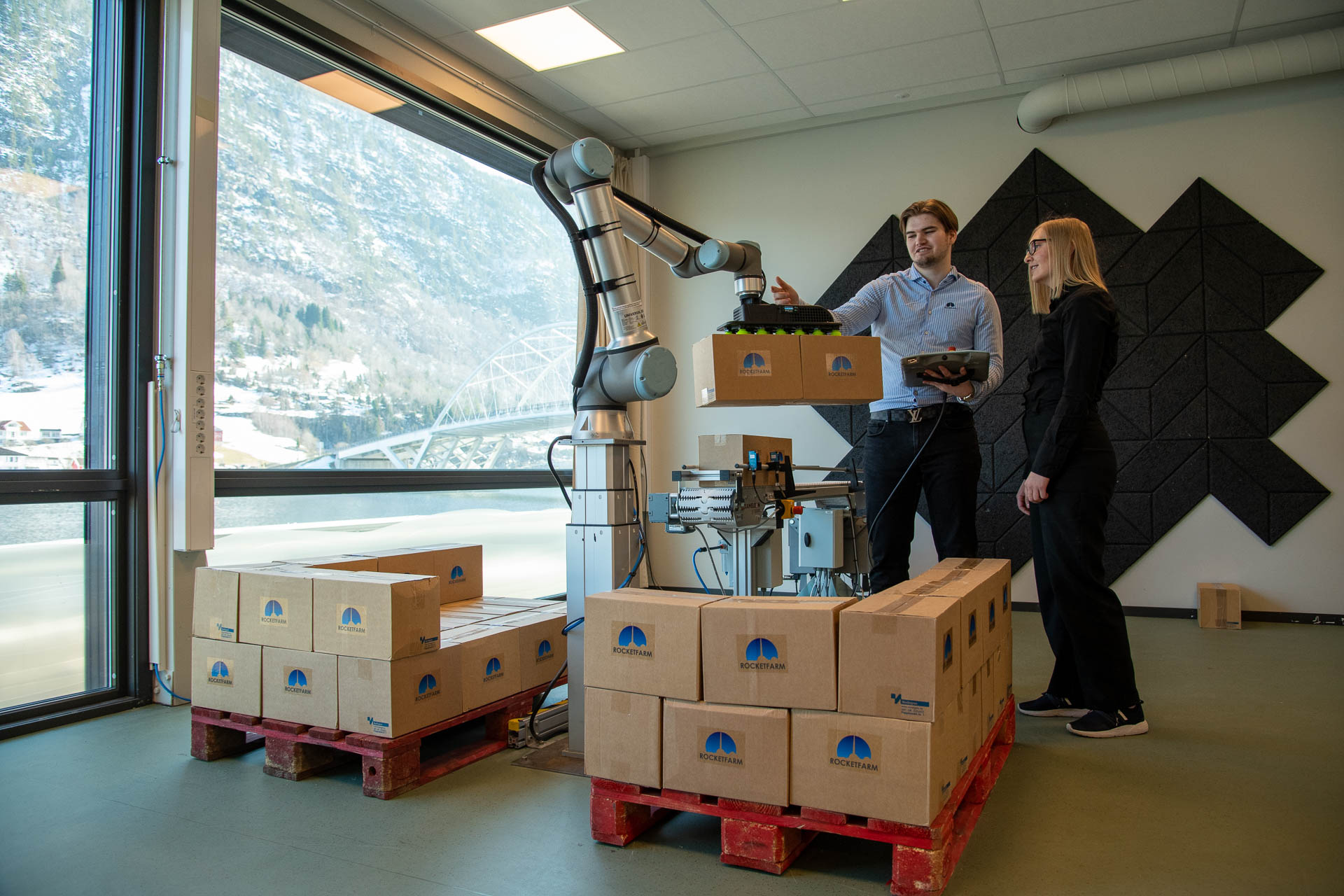
Our depalletizing software, dPally, is specifically designed for Universal Robots collaborative robots and offers a wide range of possibilities. This article is a must-read if you’re looking to improve efficiency, cut costs, or streamline your operations. Here, we’ll explore the pros and cons of using dPally, so you can decide whether it is for you or not.
More complex than palletizing
Before we dive into the ‘how’ and ‘where,’ let’s start with the ‘what’ of MRC Fast Track.
To begin this article with some factual information, it would be helpful to clarify what depalletizing entails. While it may appear to be the opposite of palletizing, it is actually a more intricate procedure and not simply a reversal of the process.
One of the most important reasons is that picking boxes from a full pallet is less accurate than picking them from a conveyor belt.
Rocketfarm’s dPally software solved this problem, as it has a controlled pick-up using the force sensors in the e-Series to overcome height and lateral tolerance.
Capabilities of dPally
You may be wondering what capabilities dPally has that make it superior. In short, depalletizing projects once seen as challenging or expensive will now be within reach with dPally.
Here are some of the software’s capabilities:
Flexibility in Weight Handling and Grip
dPally were made to handle items weighing up to 20 kilograms, including the weight of the gripper itself. This capability allows the UR robot to tackle a wide range of products, from smaller and lighter items to heavier ones.
By handling such a diverse weight range, dPally can cater to different businesses operating varying product sizes and weights, making it a flexible solution for customers with various depalletizing needs. Please note that the boxes can have varying weights, but it is essential to maintain uniform box dimensions on each pallet. One can adjust the various weights using the callback function on the UR robot’s teach pendant.
Vision-Free Precision
Camera systems can be expensive to install and integrate, requiring specialized calibration and regular maintenance. One of the standout features of dPally is that it eliminates the need for visual recognition, enabling businesses to achieve results without the burden of expensive vision technology. The vision-free approach reduces costs and enhances reliability in depalletizing operations.
With advanced algorithms and sensors, dPally can accurately detect and handle products, leading to a more efficient and dependable depalletizing process while minimizing the risk of errors and downtime.
Overall, the no vision feature enhances the cost-effectiveness, reliability, and ease of use of dPally, making it a compelling choice for businesses seeking precision in their depalletizing tasks.
Seamless Hardware Compatibility
Seamless hardware compatibility is one of the key advantages of dPally that sets it apart in the world of automation. This adaptability makes it a versatile solution that can easily integrate into existing setups, ensuring a smooth and hassle-free transition to automated depalletizing.
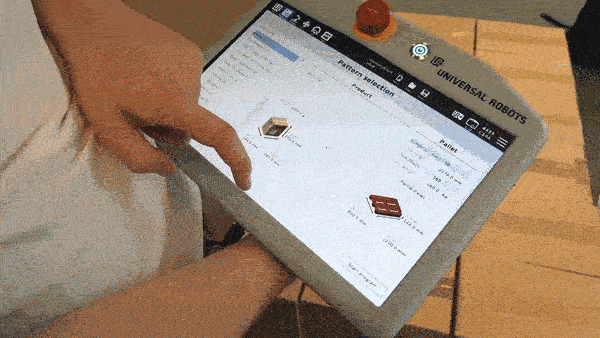
One of the concerns when implementing new automation systems is the compatibility with the existing hardware and infrastructure. Many businesses already have established setups with UR robots and various components, including conveyors, grippers, sensors, and lifting columns. Integrating a new depalletizing system may require significant modifications or replacements of these components, leading to added costs and complexities.
However, dPally addresses this issue effectively by being compatible with a wide range of hardware components commonly used in the industry. Its design allows for seamless integration into existing systems without requiring extensive modifications, reducing the implementation time and minimizing disruptions to ongoing operations during the transition.
dPally provides seamless hardware compatibility to help businesses make the most of their existing investments in automation infrastructure – optimizing their resources and maximizing their return on investment. Adopting dPally is a cost-effective solution that eliminates the need for additional expenses associated with hardware upgrades or replacements.
Overall, dPally’s seamless hardware compatibility is a significant advantage that makes it a practical and attractive depalletizing solution for businesses looking to enhance automation without disrupting their current operations. This adaptability ensures that dPally can seamlessly fit into various setups, optimizing productivity and simplifying the transition to automation.
Multi-Pallet Support
Unlike traditional systems limited to one pallet at a time, dPally excels at managing one or two pallets simultaneously, even with varying sizes.
For high-volume businesses dealing with multiple pallets of different sizes, dPally offers a significant advantage. It streamlines depalletizing, reducing downtime and boosting productivity. Handling one or two pallets optimizes throughput and minimizes robot inactivity, ensuring a smooth flow of products.
This feature allows businesses to consolidate operations and streamline workflows, resulting in cost savings. Industries with high-volume depalletizing requirements benefit from this practical and efficient solution, which ensures continuous operations, improved productivity, and reduced equipment needs.
Dual Product Mode
A remarkable feature of dPally is its ability to depalletize in Dual Product Mode, meaning that the software can simultaneously transfer boxes from two pallets onto two conveyor belts. The feature is a remarkable capability that sets it apart as an efficient and high-productivity depalletizing system.
By handling two pallets at once, dPally optimizes throughput and reduces time, maximizing the overall efficiency of the depalletizing process. This results in a more continuous flow of products, reducing bottlenecks and streamlining material handling operations.
The Dual Product Mode enables businesses to handle higher volumes of products within the same time frame, leading to increased productivity and output, which will be especially beneficial for industries with high-demand production schedules or time-sensitive operations. In addition to the productivity benefits, the Dual Product Mode can also lead to cost savings, as businesses may reduce the need for additional depalletizing equipment or labor. Overall, dPally’s Dual Product Mode will significantly enhance productivity and material flow.
Effortless Pallet Height Handling
Many depalletizing systems may struggle to handle tall pallets, leading to inefficiencies and potential product damage. However, dPally’s advanced technology and design allow the robot to manage more elevated loads smoothly, ensuring a seamless and reliable depalletizing process.
Depending on the size and arrangement of the boxes, dPally can handle items with heights up to approximately 2.5 meters. A standard setup of a 900 mm-1400 mm lifting column attached to a UR10 and UR20 further contributes to dPally’s effortless pallet height handling. This lifting column provides the necessary support and stability to accommodate most pallet sizes.
While effortlessly handling pallets above two meters in height, dPally offers businesses greater flexibility and adaptability in depalletizing operations. This feature reduces the risk of product damage during the depalletizing process.
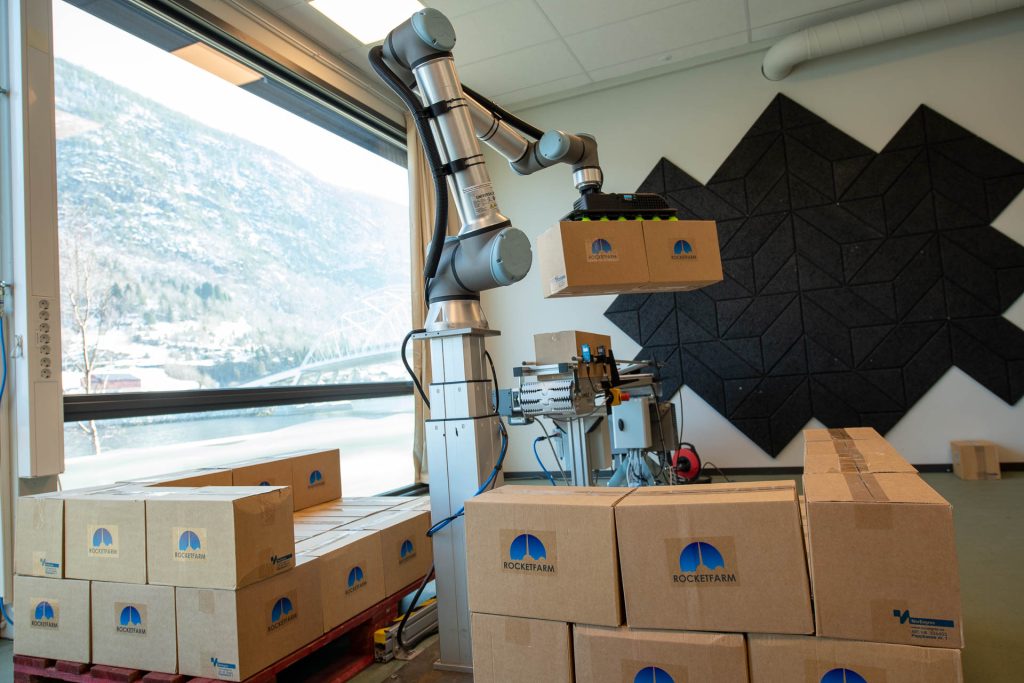
Boundaries of dPally – and how to overcome them
Life is not all about benefits – and dPally is no exception. Although it offers impressive capabilities, certain limitations must also be considered, as well as the strategies to overcome them:
Pallet Accuracy
Pallets may not be perfectly aligned during stacking, loading, or transport because of slight lateral variations. The lateral positioning can still be acceptable, and the lateral tolerance is the allowance for these minor deviations. It limits how much the items can deviate from an ideal, perfectly aligned position on the pallet while still being considered acceptable and safe for depalletizing.
To address this challenge, dPally uses a controlled pick-up strategy, leveraging the e-Series robots’ force sensors, ensuring accurate depalletizing even with height and lateral tolerance challenges during transportation, making dPally more advanced than its “sibling“, Pally.
By implementing the controlled pick-up strategy, dPally enables the robot gripper to detect and assess the allowable margin of error in positioning or aligning items during the pick-up process. With its advanced technological capabilities, dPally ensures precise and accurate pick-up of boxes, even in slight variations in the horizontal alignment of items on the pallet.
Speed Consideration
When using Force Mode to pick up items during depalletizing, it may slow down the overall process, which can affect the number of boxes that can be depalletized in a given time frame.
However, with the use of dPally, speeds of up to 30 cases per minute (CPM) can be achieved, which is significantly higher than what is possible without dPally or its competitors.
Reach Constraints
Reach Constraints refer to a limitation in the range of motion or distance the robotic arm can generally extend to access objects on a pallet. When picking up boxes, the robot may need to raise them to avoid obstacles before placing them on the conveyor belt.
With dPally’s standard setup, which includes a lifting column ranging from 900mm to 1400mm, it can even depalletize high pallets that are roughly around 2.5 meters high, depending on the boxes’ size and pattern. This setup determines the vertical distance that the robot can reach when picking up boxes.
Gripper Size and Orientation
Gripper Size Consideration:
It’s crucial to avoid using a gripper larger than the boxes handled in the depalletizing process. If the gripper is too big, it may not fit properly around the individual boxes, and as a result, it could grip multiple boxes at once or grip parts of neighboring boxes.
The gripper size should be proportional to the dimensions of the box. Additionally, the gripper should be able to activate different zones during the depalletizing process.
Gripper Orientation:
In addition to selecting an appropriately sized gripper, the orientation of the gripper while approaching and gripping the boxes is critical. We recommend letting dPally define the gripper orientation automatically rather than setting it manually.
By allowing dPally to determine the orientation of the gripper, the robot can approach the boxes as efficiently and effectively as possible. The software’s algorithms and logic have been optimized to understand the dimensions and positions of the boxes, allowing the robot to pick them up accurately and securely, minimizing the risk of misalignments or unintended box movements during the pick-up process.
By letting dPally handle the gripper orientation, the depalletizing process becomes more streamlined, reliable, and less prone to errors caused by manual adjustments.
dPally’s niche
Although dPally is an ideal solution for small and medium-sized enterprises that use collaborative robots to improve safety and efficiency, larger logistics companies may require even greater customization and flexibility.
These companies often have unique and specific needs that demand highly customizable depalletizing solutions. They may handle unconventional pallet configurations, non-standard packaging, or fragile items that require specialized handling. Therefore, dPally’s standardized capabilities on a UR collaborative robot may provide a different level of flexibility and customization than these companies need.
The new era of depalletizing starts now
dPally paves the way for a new era of depalletizing excellence with its advanced technical features and commitment to hassle-free automation.
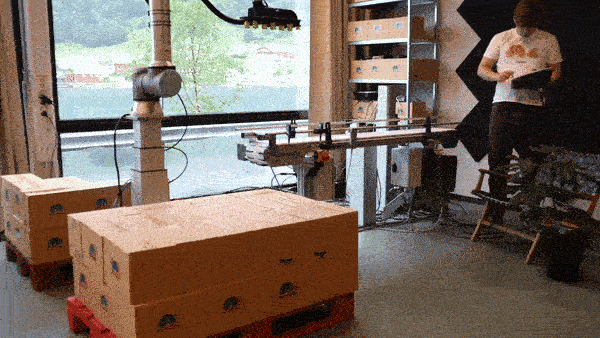
Gain in-depth information about the solution, sign up for a 30-day dPally trial, and connect with our team for further details. Be at the forefront of effortless automation and seize this opportunity to enhance productivity.
Get in touch
Get in touch today if you’d like to know more about how dPally can benefit your business or if you’d like to offer dPally to your customers.
Brigt
Channels Executive
brigt.roysum@rocketfarm.no
