In this article, we’ll go through what you need to think about when putting together a palletizing solution, in addition to providing some insights on how you can make the best choices for your production line.
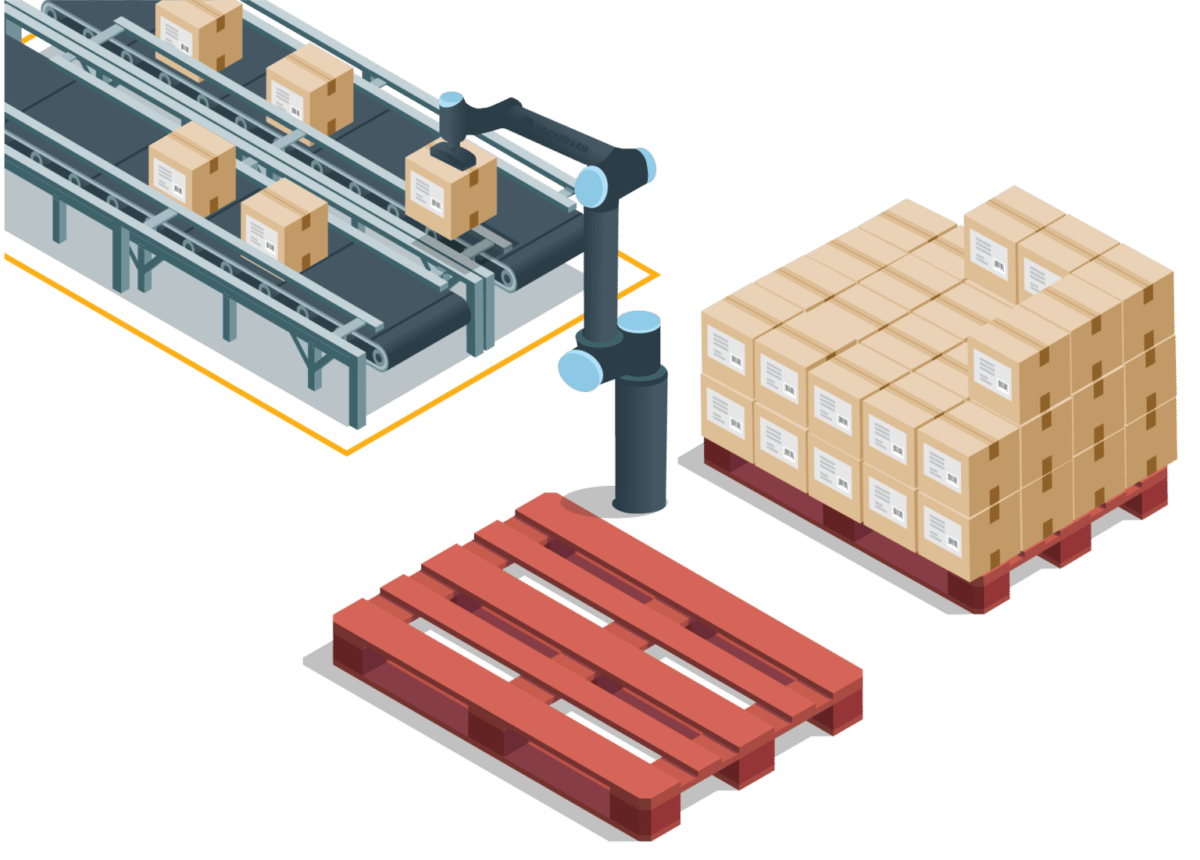
What is a palletizing solution
A palletizing solution can make a huge difference in the efficiency and effectiveness of your production line. A well-thought-out and configured solution has to account for a range of components.
The minimum requirements include a robot, a fixed pedestal or lifting column, a gripper, a conveyor, sensors, and a teach pendant. This mix, coupled with palletizing software, creates a complete solution.
To make the best choice for your production line, you should consider the following factors:
Robot
The selection of a suitable robot involves a detailed assessment of payload capacity, reach, footprint, and safety. Below, you will find a couple of things to consider on each part.
Payload: This consideration is very much dependent on the weight of the boxes you intend to palletize. For boxes weighing less than 12.5kg, a UR10 robot could be sufficient. However, if you need to palletize a significant number of boxes per minute or heavier boxes, you might require a robot with a higher payload capacity, such as the UR20.
Reach: The reach of your robot is dependent on the requirements of your palletizing task. Factors such as gripper type, palletizing pattern, layers, hardware configurations, pallet type- and dimensions may also affect reach. It’s essential to ascertain the ideal reach to avoid complications.
By clicking here, you can read more about how to solve issues connected to the reach.
Footprint: Space requirements can be vital in determining the choice of the robot. The area you have available for the installation of the robot should be carefully evaluated to ensure the efficient use of space.
Safety: This consideration involves extra sensors and fencing to ensure the safe operation of the robot. The type of safety measures to be employed will depend on the specific requirements of your production line.
Read more about safety settings here.
Frame
When selecting a frame for your robot, it is important to consider the available space and decide whether it should be mounted on a fixed pedestal or a lifting column. This decision should be based on your pallet requirements and facility layout.
Gripper
Selecting the appropriate gripper for your cobot is a crucial decision that requires careful consideration, taking into account the specific requirements (such as multi-pick capability, box type, size, and surface) and what type of robot is involved.
Grippers can be categorized into foam, suction cup, and pinch grippers:
Foam grippers adapt to varied box sizes or uneven surfaces thanks to their adhesive properties. They are therefore proven to be a good choice in production lines with various sizes and surfaces of boxes.
Suction cup grippers are ideal for cases where box quality varies. These grippers allow accurate gripping at specific points in order to pick the boxes where they are the strongest or provide the best vacuum.
Pinch grippers are best for heavy production lines or boxes without lids, often used for bottles or other fragile production lines.
Conveyor
When it comes to the conveyor, a nice thing to notice is that Pally can handle the conveyor from the front as well as from the left and right. Finding the distance from the robot to the conveyor is important to avoid collisions and enable multi-pick.
Setting the right conveyor height is also crucial to achieving the most effective robot movement. It is recommended to set the height between 700 and 800mm for optimal performance when palletizing patterns below approximately 1,8 meters. A higher height for the conveyor can increase CPM if you palletize patterns higher than that.
Software
To streamline the palletizing process and improve efficiency, implementing palletizing software like Pally can be a game-changer.
With digital twin simulations, you can test various hardware components and total solutions to make informed decisions and achieve a top-notch palletizing solution. To learn more about this cutting-edge technology, click here.
In conclusion, assembling a great palletizing solution involves an approach that takes into account all the components and their potential connections. Making the right choices for your production line can significantly enhance productivity and efficiency.

Sign up for our newsletter and get a FREE ebook
By signing up for our monthly newsletter, you’ll get case stories, product launches, and tips to automate your production line!
Additionally, you will instantly receive an ebook about implementing palletizing. For more information, please visit our newsletter subscription page.
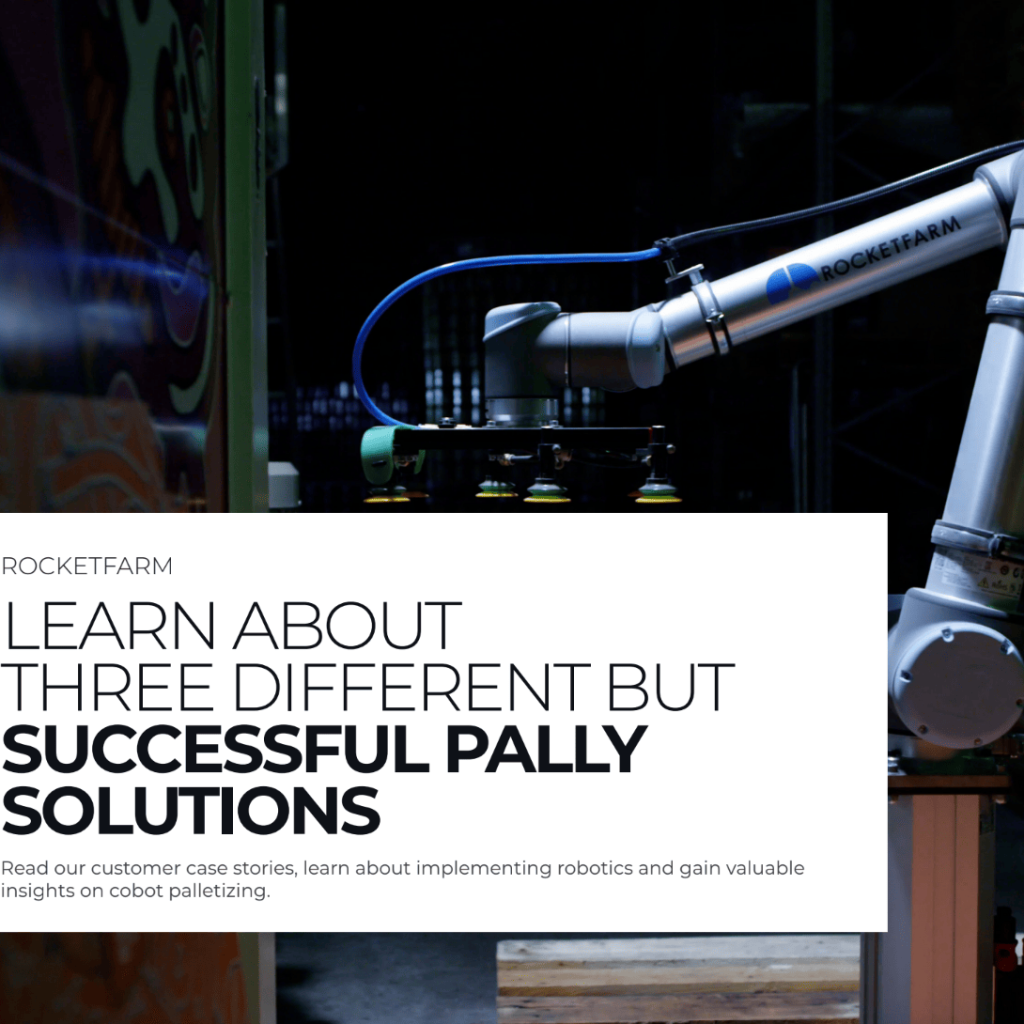